Follow-up of worksite equipment: Best practices!
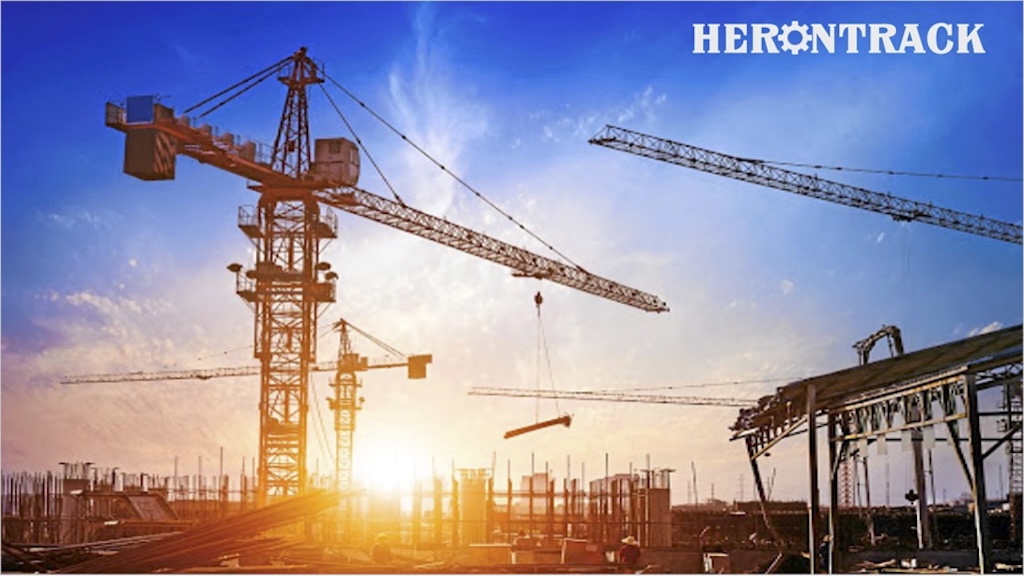
On a construction site, efficient material management is essential to ensure productive, safe and profitable operations. Between tools, personal protective equipment (PPE) and machinery, it's crucial to know where everything is, what condition it's in, and whether it's available when needed. Yet many companies in the construction and public works sector are experiencing difficulties due to loss, theft or inadequate maintenance of their equipment, resulting in delays and extra costs.
Thanks to tracking technologies and digital solutions such as GPS and management applications, it's now possible to have a clear, real-time view of your inventory. This article explores best practices for optimal on-site equipment tracking, as well as the concrete benefits these new solutions bring to industry professionals.
Why is equipment monitoring essential?
On a construction site, equipment is often dispersed, shared between several teams and used on different sites. Common challenges include
The main issues involved in tracking equipment :
Loss and theft of equipment
On a construction site, equipment is often moved between different areas, used by several teams, and sometimes left unattended. Lack of traceability leads to :
- Substantial financial losses due to lost equipment.
- Thefts that require equipment to be bought back, increasing unforeseen costs.
- Lost time tracking down missing equipment, delaying operations.
Lack of visibility on equipment status
Equipment must be regularly inspected and maintained to ensure that it is in good working order and complies with safety standards. Failure to do so can result in :
- Accident risks: an unchecked harness or defective scaffolding can endanger workers' lives.
- Site interruptions: if a key tool breaks down and no preventive maintenance has been carried out, work can come to a standstill.
- Unforeseen repair costs: poorly maintained equipment wears out faster and requires more expensive repairs.
Poor inventory and availability management
Lack of visibility on available equipment leads to inefficiencies
- Unnecessary orders: duplicate purchases due to lack of accurate inventory.
- Longer lead times: waiting for equipment to be released or replaced.
- Confusion between teams: not knowing who's using a tool or where it's stored.
The HeronTrack solution: intelligent, automated management
HeronTrack simplifies on-site equipment management with GPS chipschips, BLE trackers, QR code labels and an intuitive mobile application. This solution helps construction companies reduce losses, optimize equipment management and improve safety.
- 📍 Real-time location: Every tool and machine is tracked in real time using GPS chips and BLE tracers.
Example: A site manager is looking for a core drill. Rather than waste time, he consults the application and sees that it has been left at another site. An employee can pick it up immediately. - 🛠 Inspection and maintenance management: The application records inspection dates and generates alerts to warn users when inspections are required.
Example: A worker is about to use a harness. The application reports that it has not been inspected recently. He takes another in good condition, avoiding the risk of an accident. - 📦 Inventory optimization Thanks to a real-time overview of stock levels, it is possible to manage reservations for missing or unavailable equipment.
Example: A manager thinks he needs to buy new scaffolding, but the application tells him that an available model is in another depot. The result: savings and better equipment management. - 🚨 Reducing loss and theft: Alerts for suspicious tool movements enable rapid reaction in the event of theft or loss.
Example: If equipment is moved outside authorized hours, HeronTrack sends an alert to the security team, preventing theft and financial loss.
Thanks to HeronTrack, companies save time, avoid unnecessary costs and secure their worksites.
Case study: a structural engineering company starts its formwork phase
During the formwork phase, a multitude of specific tools and equipment are used. The risks of mismanagement, such as site delays or accidents, are high.
Before the start of the formwork phase, the site manager opens the HeronTrack application to check that all the necessary equipment is available:
- He consults the list of registered equipment (molds, scaffolding, specific tools) and checks their location.
- The application tells him if any equipment is missing or requires maintenance before use. If this is the case, it reserves an available tool or sends for a missing piece of equipment.
In just a few minutes, all material management is completed, enabling the formwork phase to start without delay, while optimizing the use of resources and guaranteeing site safety.
Conclusion
Tracking site equipment is fundamental to ensuring the safety and efficiency of projects in the construction industry. Faced with the challenges of loss, theft and equipment management, it's essential to adopt modern solutions to optimize operations.
HeronTrack offers real-time tracking technology that enables companies to locate their equipment, manage maintenance and ensure compliance. This helps create a safer working environment while reducing site interruptions and optimizing costs.
Investing in a solution like HeronTrack is not just a logistical improvement, but a strategic choice that helps maximize project profitability. By adopting this technology, companies can ensure that their worksites run safely and efficiently.
Choose modernity and safety with HeronTrack! 🚧