Inventory management, how to optimize for equipment and tools: Advanced solutions for companies with mobile teams
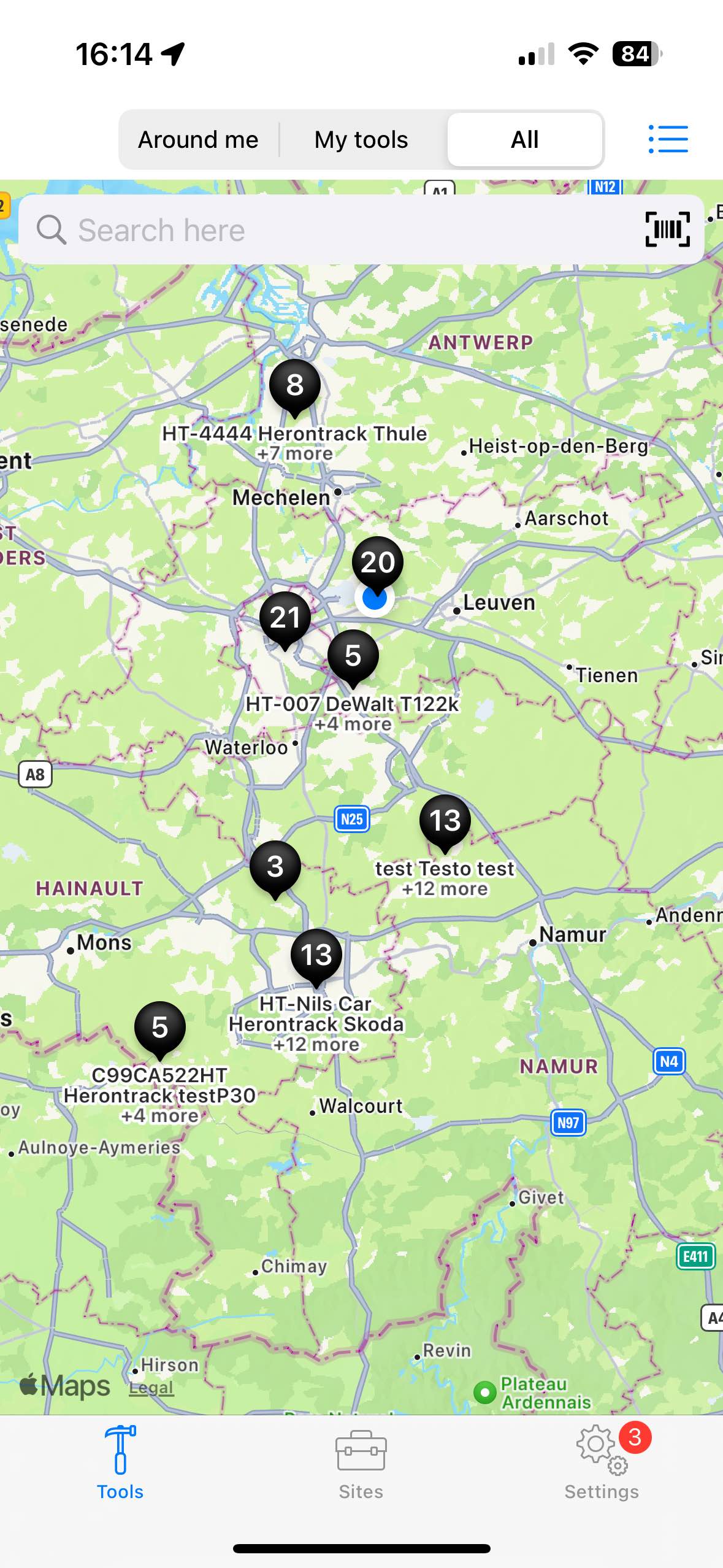
What do we understand by inventory management?
In terms of inventory management, we can already draw a distinction between consumables (goods that are consumed, such as wood, metal, screws and other products needed to carry out our activity, and which are taken out of stock and never returned, and therefore consumed) and equipment (tools, which are used to carry out our activity, but which are returned to stock or to the depot or to the van (mobile stock)). The complexity of managing from one to the other, and the need for it, are not the same. In this article we focus on inventory management for equipment.
Effective inventory management is crucial for any company seeking to improve operational efficiency and maximize profits. Whether you're managing a fleet of equipment or a stock of tools, good inventory management helps reduce costs, improve customer service, minimize surpluses and stock-outs, and optimize the use of resources.
The challenges of equipment and tool inventory management
Companies large and small face a variety of challenges when it comes to managing their equipment and tool inventories:
1. Precise inventory tracking:
Keeping accurate track of available equipment and tools is often a complex task, especially when these assets are spread over several worksites or job sites.
2. Anticipating demand:
Predicting future demand requires accurate data and rigorous analysis to avoid shortages or surpluses.
3. Avoid excess inventory:
Excess equipment or tools can lead to high storage costs and asset depreciation.
4. Prevent stock-outs:
Out-of-stock situations can lead to work stoppages, lost sales and customer dissatisfaction.
HeronTrack solutions for equipment and tool inventory management
At HeronTrack, we understand the challenges faced by companies with mobile teams on different job sites. Our GPS tracking solutions provide real-time information, enabling optimal control of assets. Here's how our technologies can transform inventory management:
Real-time location monitoring of equipment and tools
One of the main advantages of GPS trackers is their ability to provide real-time location data for every piece of equipment and tools. This feature is particularly useful for companies with mobile teams operating on various worksites. Thanks to this technology, you can :
- Maximize asset utilization: Make sure every tool or piece of equipment is used where it's needed, reducing downtime and improving productivity.
- Improve job site planning: Knowing where your equipment is located and its availability, you can better allocate your resources and plan your activities.
- Avoid unnecessary rentals: Precise data can help you avoid renting equipment unnecessarily, especially when it's simply waiting in a vehicle on a construction site.
Equipment theft prevention and recovery
Equipment theft represents a major financial loss for many companies. Our GPS solutions help prevent such incidents and recover assets quickly:
- Georeferencing and instant alerts: Define specific geographical zones for your worksites. If a piece of equipment leaves these zones, you receive an immediate alert.
- Rapid asset recovery: In the event of theft, precise GPS data facilitates rapid location and recovery of stolen equipment, minimizing losses and downtime.
Equipment and tool maintenance planning
Our GPS trackers don't just track location; they also provide information on equipment use:
- Real-time usage monitoring: Track operating hours to better understand tool wear and plan proactive maintenance.
- Optimized preventive maintenance: Plan maintenance in line with actual equipment use, thus extending service life and avoiding costly repairs. Read more on the subject in our April article.
Inventory accuracy and reliability
Accurate inventory management is essential for operational efficiency and compliance with regulatory requirements:
- Automatic updates: GPS tracking systems automatically update inventory in real time, reducing human error and the need for manual checks.
- Complete audit trail: Keep a detailed record of the movements and use of each piece of equipment to facilitate audits and ensure compliance.
Lower operating costs
By optimizing equipment and tools management, you can significantly reduce your operating costs:
- Lower insurance premiums: GPS-enhanced safety measures can lead to lower insurance premiums for your company.
- Reduced losses and replacement costs: Effective monitoring reduces the risk of equipment loss, thus avoiding high replacement costs.
Business process improvement
Integrating GPS tracking into your inventory management systems simplifies day-to-day operations:
- Integration with ERP systems: GPS data can be synchronized with your enterprise resource planning (ERP) systems, providing an overview of equipment and requirements.
- Informed decisions: Access real-time data to make strategic decisions on resource allocation and equipment deployment, increasing the overall efficiency of your operations.
Conclusion
For companies that depend on equipment and tools for their day-to-day operations, HeronTrack solutions represent a strategic investment. By providing real-time visibility, enhancing safety and optimizing maintenance, our GPS trackers ensure that your assets are used efficiently and remain in good condition. Adopting GPS technology for equipment and tools inventory management not only ensures accurate asset tracking, but also boosts your company's performance by reducing costs and optimizing resources.