Tool inventory, do you always have an accurate inventory? Yes, we do
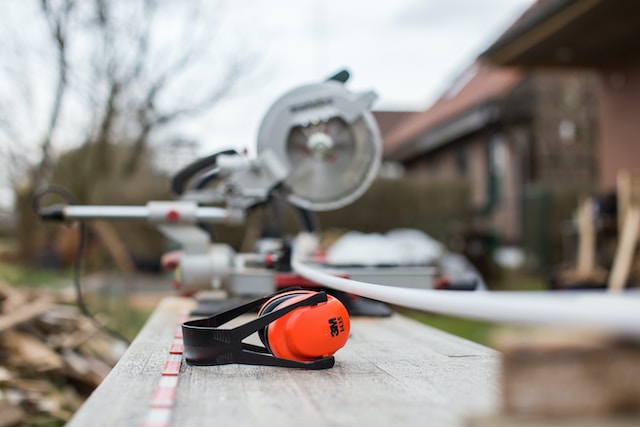
Your tools are an essential part of your business. That's why it's important to maintain an accurate and complete tool inventory. This way, you know exactly where your tools are at all times. In this article, you'll discover how to easily create a reliable tool inventory that will save you time and money.
What is a tool inventory?
A tool inventory is a detailed list of all your tools and equipment. An inventory contains detailed information on your equipment, such as date of purchase, type and status, serial numbers, maintenance history, last user and much more.
A complete and accurate equipment inventory is one of your company's greatest assets. It makes your organization more productive and helps you save money.
Why do you need a tool inventory?
Keeping an accurate tool inventory has many advantages for your company. Here are some of the most important.
1. Know what you have
With an inventory of all your tools, you have a complete overview of all your equipment. Precisely tracking the state of use and location of your tools, you know exactly what equipment is still available for future projects ; more, you can anticipate what you'll need in the coming period to keep your business running smoothly and your projects.
2. More information on how to use the tools
It's useful to know which tools your company uses the most, which equipment breaks down the most, which have the lowest hourly costs and which have high maintenance costs.
Taken together, these data provide important information for future purchases.
3. Optimize your schedule maintenance of your tools
By keeping an accurate record of the maintenance history per machine in your tool inventory, you know exactly when it's time for a new service. Well-maintained tools last longer and save you a lot of money. What's more, you reduce the risk of unscheduled downtime due to faulty equipment.
4. Increase your staff's sense of responsibility
Many tools are lost due to inattention or laxity on the part of staff. You can avoid this by including the names of the latest users in your tool inventory. This way, your employees know that tool use is closely monitored, and their sense of responsibility towards your tools grows.
Features of a reliable tool inventory
In many companies, tool inventories have long been kept with pen and paper. To find out who was using a particular device, the name of the user was entered on a form. Today, many companies work with a digital spreadsheet, but this too has its limitations. It takes a lot of time and effort to keep your inventory list up to date.
And that's what it's all about: if your inventory isn't right all the time, it's worthless.
Your inventory must therefore meet the following criteria:
- Complete : all your tools must be included
- Precise : contains sufficient details about your tools (location, last user, history of maintenance, ...)
- Up to date : any changes in the field must be incorporated immediately
A complete and accurate tool inventory: how do you go about it?
Keeping a tool inventory with pen and paper or a spreadsheet is not a good idea. It's better to opt for a user-friendly inventory system that adjusts every change automatically and in real time. This is the only way to ensure that your inventory is complete, accurate and up to date at all times.
HeronTrack is a comprehensive yet simple tool tracking and inventory software that automates all the work in the background. This way, you can concentrate on the things that really matter.
How does the automated tool inventory of HeronTrack work?
Tracking your tool inventory is easy with HeronTrack.
Automatic tool detection
Each tool is fitted with a small sensor. A fixed gateway detects which tools are present in the depot and transmits this information automatically and in real time to the online platform. The depot manager will never again need to clock tools in and out. What's more, the warehouse manager can consult all tool data in the field: user and location history, maintenance and inspection reports, etc.
Tool reservation via mobile app
Your workers can reserve the tools they need in advance via a convenient mobile app. This way, they always have the right equipment at hand and can get to work straight away. Without delay.
The equipment manager can manage all requests and reservations in the planning module online or on his smartphone.
Maintenance and usage history
HeronTrack keeps a history of device usage and of device maintenance. This way, you know when a device needs servicing or replacement. The equipment manager automatically receives notification when a device needs new service. This helps keep your tools in top condition.
Start now with HeronTrack software
HeronTrack is the ultimate digital tool for tracking, inventorying and managing all your tools. This allows to keep your depot inventory always up to date, your processes more efficient and you save costs.
Would you like to get started with HeronTrack's automated tool inventory today? Order your version now at https://herontrack.com/caracteristiques/.